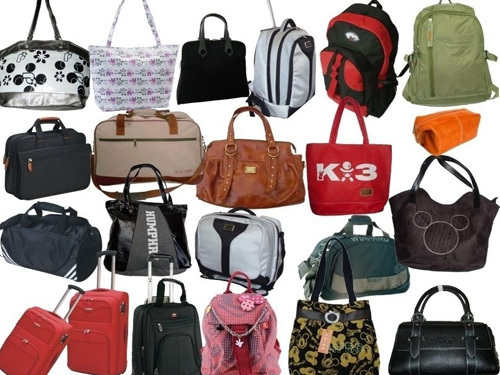 服装箱包品牌企业,是一个时尚行业,有时候拼的就是时间,谁最先上新款、谁的翻单速度快,就能抢占先机,获得更多销售机会带来更大利润,同时减少企业库存,让现金流更充足。快速,不仅仅只是要求营销的反应能力,关键点还要看生产供应链的反应,如果不能按需要时间交货,一切都是空谈。
在企业之间,谁都希望准时进货出货,少占资金。在企业内部,首先是交货时间。那“不准时”掩盖了什么?比如:用超量库存防止工期延误。在时间博弈中,企业既想要拉住用户,又不想蚀本。可对时间的重视,往往是在受到不准时惩罚之后。关键是,我们能超前吗?能提高企业生产供应链快速反应的竞争力吗?
我们都知道,一个企业的竞争优势是多方面的,比如价格优势、质量优势、性能优势等,随着市场竞争的加剧,对产品的交货期要求是越来越高,因为市场瞬息万变,经销商在一个月后拿到产品时,可能市场情况已经发生变化,这种产品旺销已过,甚至已经变为滞销。对于销售来说,最希望随时订货随时有货,许多企业在“客户”是上帝的理念下,为了满足客户的需求,保持有1-2个月的材料、成品存货。表面上看虽然能做到随时订货随时有货,但因为保持有大量的存货,占有巨额流动资金,削弱了企业的赢利能力。另一方面无论是材料还是成品,大量存货风险极大,因此而导致企业陷入困境甚至倒闭的事例并不难找。为了规避风险,同时又要尽量适应市场的变化,一个好的办法就是通过精益生产来缩短交货期。
能否超前,提高竞争力?我们需要先算一笔帐。人财物要付出多少才能换来准时,值不值。问题的实质在于:有多少潜力可挖?不挖会怎么样?怎么挖?
有多少潜力?这个问题相对简单,对生产绩效做认真的测量分析就可以。不挖会怎么样?
这个问题不简单!时间背后的复杂矛盾,形成了浪费,这是不争的事实。
但是,存在是合理的。生产企业在实际运作中逐渐形成了一套规则和浅规则。它在保证产品能造出来的同时也使浪费合理化。挖潜意味着要在上一个台阶后建立新的合理。
另外,随着消除浪费的工作不断深入,需要更多的规矩来规范运作。比如,为了保证质量(时间在生产运作中也具有质量特性),就需要稳定。稳定和变异是对立的,变异可能带来次品,也可能带来意外的惊喜。但为了企业的总目标,也为了简单,只有把变异限制在尽可能小的范围里。不过,挖不挖,关键看竞争压力。要再降低成本,打造柔性快速反应的能力,时间管控能力是基础。甘蔗没有两头甜。怎么挖?
这很实际。不管能挖出多少?能挖到什么好处?会挖最重要。
改进时间的管控能力有两种途径,一步到位或者逐步改进。从实践角度看,逐步改进是现实的选择。这样可以兼顾正常的生产秩序。要想从中获益涉及了方方面面的工作,它不像质量改进那样可以零打碎敲的搞。另外,生产永远有问题,理想状态是我们努力的方向。关键是,目标和实际可能之间怎么来妥协。企业最清楚自己能做什么。只是要弄清楚整个改进路线的脉络,清楚每一次的奋斗目标会触及哪些问题,时时知道我们距离理想状态还有多少差距。
要想从改进中获益需要方法。到目前为止,解决数量的方法远多于时间。时间问题是动态问题,本身就难处理。在技术中最容易出问题的就在动态方面。虽然有些企业基本上能控制产品质量,但始终没有明白动态问题的控制思路,甚至连变化趋势都不曾记住。在运作管理中,这同样也是一大障碍。为了简化问题,采取这样的方式:当每个阶段的工作结束后,总结查找存在的问题和原因,避免重复出现。一般,在不同的管理台阶上,关键性的问题不很多。这样将动态问题用静态的方法来处理。我们选择做事后诸葛亮,而不是做事前诸葛亮,或者事中诸葛亮。要想缩短生产周期,提高生产快速反应能力,我们必须结合精益生产,做到:精益的一个流生产100道工序,总加工时间只要125分钟,1000件产品,却从裁剪到班组生产完成第一件成品下线,花了2-3个工作日。这样的情况在国内服装箱包行业还十分普遍。如此长的“生产”过程,企业恐怕没有统计过因此而流失了多少没有“耐心”的客户。在精益生产中,将不能产生附加价值的诸如搬运、存储、检查等视为浪费,因此,缩短生产周期的出发点就是要排除这些浪费。理想的方法就是从第一个工序一个一个地通过后面的工序,即所谓的单件流生产。关于单件流生产,在推行过程中要注重7个要点:
(1)单件流动“单件流”生产的条件,首先是由单件流动开始的。单件流动就是仅做一个、传送一个、检查一个,将原材料经过一个个的加工工序而做成成品。这种工作看起来很简单,其实并不简单,也没有一定的模式可循。
(2)按加工顺序排列设备但要注重的是,单件流生产并不要求将车间所有的设备都连起来,部分连接也是可取的,甚至对于特殊的工序,比如有多种产品需要使用设备,或是比较昂贵的特殊设备,可能并不合适放在只生产某一个产品的生产线中,而是做为共用使用。
(3)按节奏时间进行生产并非生产越多越好,越快越好,应该根据市场的需求经常调整生产节奏。关心的是“我们今天需要生产多少”,而不是“我们今天能生产多少”。
(4)培养多能工很多公司虽然都是在运用U型生产线,但操作人员却是固定在某台设备上作业,这样的方式虽然能减少中间存货,但无法根据产量大小调整人数。
(5)使用小型、便宜的设备或辅助工具这一点也是国内许多服装箱包企业感到困惑的地方。国内许多企业一直在追求大型的设备、通用(多功能)的设备,结果是治理起来困难,使用效率不高,或者造成半成品大量堆积。小型的设备移动起来方便,有利于根据市场的变化进行调整布局。我们曾经指导过的一家企业,使用价值30万元的一台全自动大型、高速的自动开袋设备,因为速度快,前工序组装只能按大批量提供,后工序也只能按大批量接收,导致中间半成品库存达1200件,并且生产周期要三天以上。我们建议购使用开袋模板,并在实施一个流生产时布置到生产线中,使得中间半成品没有存货,生产周期只有5分在,大幅度缩短了交货期。
(6)“U”型布置如果将生产设备一字摆开,工人从第一台设备到最后一台设备就需要走动很远的距离,从而造成严重的人力浪费。因此,“单件流”生产要求将生产设备按照“U”字型来排列,从入口到出口形成一个完整的“U”型,这样就可以大量的减少由于不同工序之间的传递而造成的走动,减少时间和搬运的浪费,增加生产效率。
(7)作业标准化作业的标准化就是要求每一个岗位、每一道工序都有一份作业指导书,然后检查员工是否按照作业指导书的要求工作,这样就能强制员工严格按照既定的生产节拍进行生产。如果作业没有标准化,那么生产一个产品的时间就得不到控制,无法控制生产节拍,更无法保证形成“单件流”。
精益生产主要研究时间和效率,注重提升系统的稳定性,50多年来精益生产的成功案例已证实:精益生产让生产时间减少90%,精益生产让库存减少90%,精益生产使生产效率提高60%,精益生产使市场缺陷减少50%,精益生产让废品率降低50%,精益生产让安全指数提升50%。所以,我们要想缩短生产周期,提升快速反应能力,首先要解决时间问题,而能解决时间问题的,首要是改变生产模式,推动精益生产,革新生产管理,才能让我们的生产供应链,更具竞争力!
|